What we do
Turnkey Operations
- Production Stamping
- Metal Fabrication
- Prototype Machining
- Tool & Die Making
- Stamping Dies
- Prototype Stampings
- Casting Trim Dies
- Complete Fabrications
- Fixtures/Gages
- Assembly
- Spot Welding
- Robotic Welding
- Production Machining (CNC)
- Surface/Blanchard Grinding
- Fiber Optic Laser, WaterJet and Wire EDM Cutting
Secondary Operations
- Paint
- Clinch Nut Staking
- E-Coating
- Heat Treating
- Plating
- Press Brake
Capacity
- 3-Shifts/7 days a week both in Stamping Department and Tool & Die Department.
- Press Capacities: 100 to 1100 Tons
- 35,000 lb Lifting Capacity
- 250,000 square feet of climate-controlled manufacturing facility
- MTM has its own fleet of trucks for delivery
Equipment List
Production: 28 Stamping Presses (100 tons to 1100 tons)
Wire EDM: 3 Wire EDM’s to support tool & die shop
WaterJet: Capabilities to cut up to 8 inch thick material
Fiber Optic Laser: Capabilities to cut sheet steel 120″x60″ and up to 1″ thick
Assembly Equipment & Fixtures: Full assembly capabilities to handle small projects through high volume complex assembled units
Welding: Spot Welding & Robotic Welding capability
Production Part Washer: Capable of producing parts to any cleanliness specification
Surface/Blanchard Grinding: Large grinders to accommodate various sized stamping dies
CNC Mills/Lathes: Various automated CNC equipment to support tool & die shop
Presses
Quality Lab
At Manitowoc Tool & Manufacturing, we invest highly in the latest & greatest of Quality Control & Testing Equipment. You can count on us to provide all quality documentation, promptly and accurately. We are committed to providing superior service, on-time deliveries, and a quality product. Continuous improvement of our processes and strong communication throughout our organization with an emphasis on customer satisfaction is our ultimate goal.
- APQP Process Controls
- Full PPAP Capabilities to Current AIAG Standards and Automotive Expectations
- Electronically Stored Inspection Data at All Phases of Production
- Automated Calibration System
- Corrective Action Process Following 8D format with 5Y Analysis
- Preventative Action Systems (5S, EPIC – Expo Process Improvement Committee, Safety Committee)
- Shop Floor Digital KPI Displays
- Supply Chain Management Program
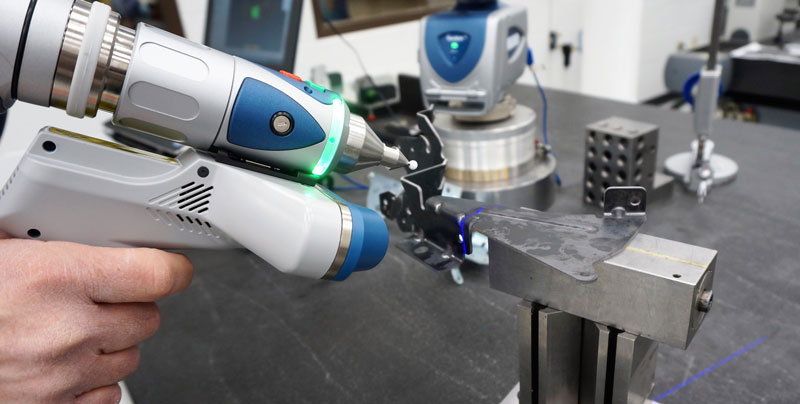
Precision. Quality.
In-house Engineering Department for Die and Fixture Design
Utilizing the following software:
- Pro/E Tool & Fixture Design
- Autocad
- IronCad
- SolidWorks/Logo Press
- Forming Analysis and Flat Blank Prediction Software
- Mastercam
- GibbsCAM
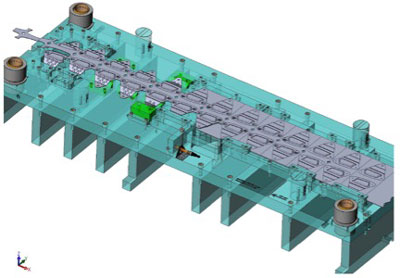
Typical Customer Profile
1,000 to 3,000,000 Estimated Annual Usages along with value-added requirements.
Additional Services
- CMI (Customer Maintained Inventories) Internal and External
- KANBAN Capable
- EDI Capable
- Cost Reduction Engineer on Staff